Loose Bolt on RV 5th Wheel King Pin Box Nearly Caused Disaster
By Guest Author: Allen Inks
I want to alert you to a close call I had with my king pin, and what I did to help ensure it never happens again.
I have an aftermarket (not original to my New Horizons trailer) king pin box that has an air bag to help the ride while towing my 5th wheel trailer. I don't think the brand is important, as the lessons learned are probably broadly applicable.
I'm pretty diligent about checking my rig before movement so I pretty sure the problem developed while driving from Denver, CO to Junction City, KS.
My king pin unit consists of an upper plate and a lower plate that are hinged together in the rear. The upper plate is fixed to the 5th wheel trailer. The lower plate has the the hitch pin fixed on the lower surface. The upper and lower plates are hinged together at their respective rear parts , and an airbag and shock aborbers are positioned between the plates at the front to absorb bumps.
The top portion is fitted down between the bent portions of the bottom plate, the holes are aligned and a hollow pivot pin is inserted through all 4 holes to form a hinge. Each end of the hollow pivot pin is threaded, and accepts a bolt with a large washer. The bolt and washer on the driver's side is to prevent the pivot pin from moving out of the hinge toward the passenager's side, while the bolt and washer on the passenger's side is to prevent the pivot pin from moving out of the hinge toward the driver's side.
A customer service rep said the bolts are to be periodically torqued to ensure they are secure. The owner's manual says nothing about this and periodic torquing would break the bond of the thread lock compound that is specified. I think the customer service rep was blowing smoke; but at least she did put me in tough with the designer (it's a small company) who told me thread lock compound (such as a LOCTITE brand compound) is to be used on the bolt threads to prevent the bolts from coming out of the ends of the pivot pin.
In any case, I didn't assemble the unit, so I don't know if the proper thread lock compound was used during assembly. I do know that I never torqued the locking bolts.
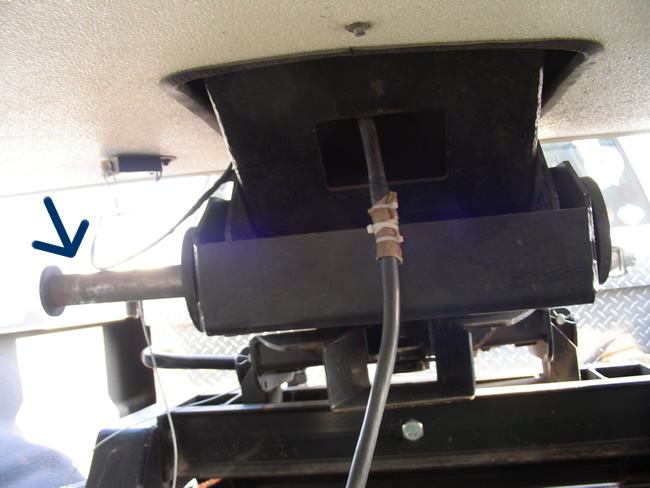
Somewhere between Denver and Junction City, the passenger side locking bolt backed out, fell into the bed of my pickup with the washer (where I found them), and the pivot pin began working it's way toward the driver's side of the hinge! The pivot pin is about 12 inches long; there was only about 6 inches left in the hinge when I found the condition. The passenger side of the hindge was completely uncoupled. The driver's side was all that was keeping the truck coupled to the trailer (apart from two shock absorbers, which aren't designed to handle the stress of pulling a 14,000 pound trailer). The upper portion pivoted to right, and began rubbing up and down as the bumps in the road came along, fortunately not doing any real damage. I suspect every bump caused the pivot pin to work further and further out of the hinge. A few more miles may have seen me testing the break-away emergency braking of the trailer as the truck and trailer came un-coupled!
After completely disassembling the hitch and evaluating the damage done, in consultation with the manufacturer, I replaced a damaged bearing, and painted the parts that had rubbed together. I then reassembled the hitch. I put thread lock compound on the locking bolts and torqued them into place on both ends of the pivot pin.
I did one additional thing that I hadn't discussed with the manufacturer. I drilled a small hole through a part of the head of each of the locking bolts so that I could insert a wire through the head of the bolt. I found two small bits of sheet metal, bent at a right angle, with a hold drilled through each. I used epoxy glue to attach each of these bits of metal to the hitch next to each locking bolt to serve as wire anchors. Then I ran safety (lock) wire between the bolt head and the sheet metal wire anchors. Now, because of the geometry of the arrangement (the lock wire is run tangent to the radius of rotation of the hole in the bolt head to the wire anchor in the direction of TIGHTENING the bolt), the locking bolts cannot rotate in the loosen direction. The photo below shows the safety-wired passenger's side lock bolt.

It's been a year now, and I've had no indication of any further problems. And no, I don't torque the lock bolt heads periodically. But I do check to see that my safety wire is in place and tight and the epoxy holding sheet metal wire anchors hasn't failed.
I can't see if the thread locking compound is intact, and don't want to torque the bolts periodically (which would break loose the thread locking compound bond) but this lock wire arrangement provides me visual assurance that the bolt isn't backing out.
Just thought I'd pass along this solution to ensure that these two "mission-critical" bolts stay in place.
NOTE: I am NOT a licensed engineer; this is not engineering advice. Every installation is probably unique. You must evaluate your own situation; you may wish to consult a licensed professional engineer to design something for you. This is just a description of a problem I had, and what I've done to address the situation - it may not be adequate, and I may have even unknowingly degraded my equipment - though I don't think so.